Firefly Welding has opened a modern fabrication facility on the Wirral. Two years in development, the space has now evolved into a fully operational, highly specialised fabrication and welding centre.
Designed to serve high-spec industrial clients across the UK and Europe, the site delivers everything from modular skid assemblies to bespoke welding habitats — all fabricated, tested, and dispatched from under one roof.
The site also includes a demonstration area for the semi-automated Firefly Welding bug and incorporates welder qualification testing capabilities.
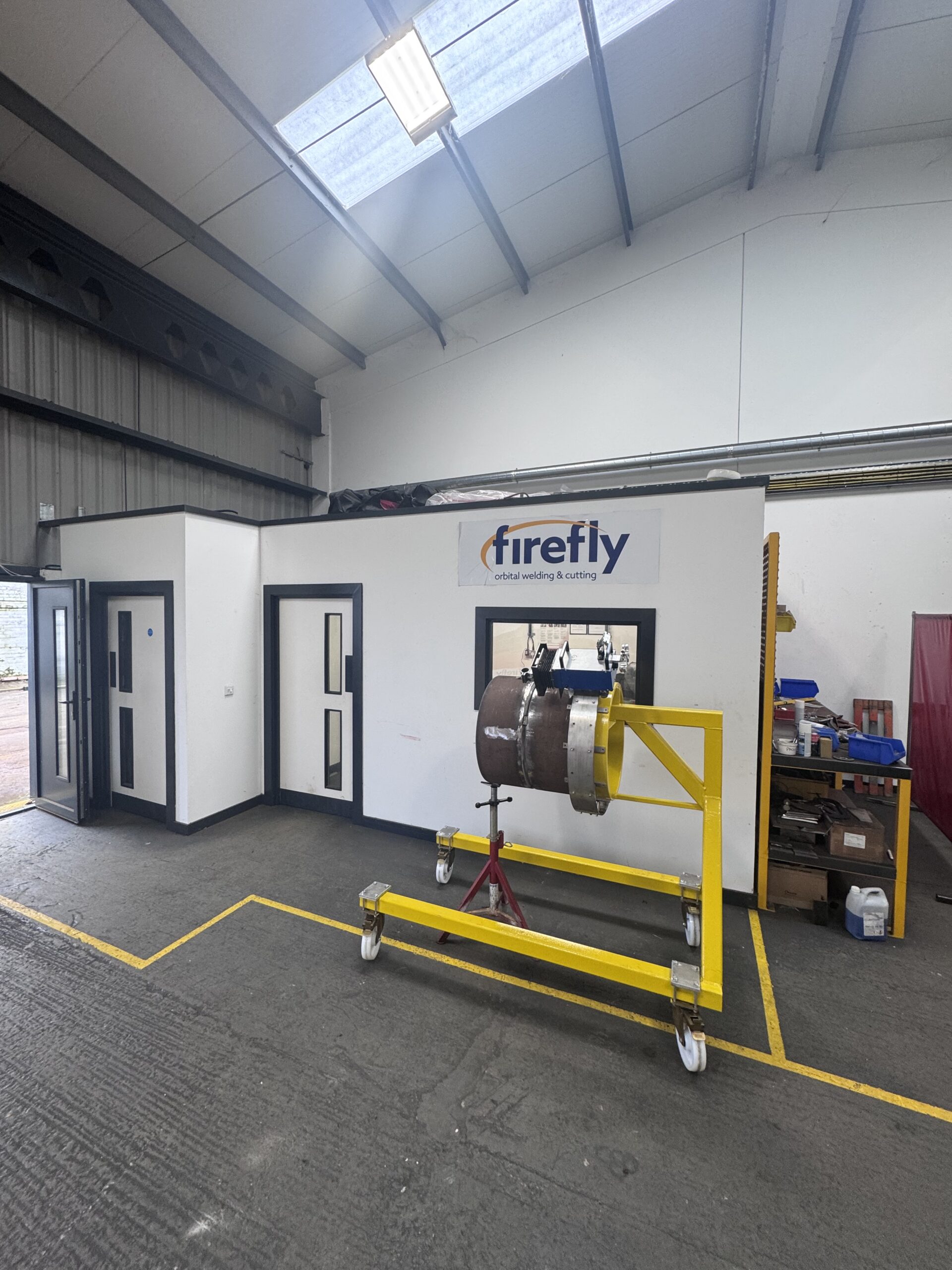
Wirral Administration and Welfare Facility
Early days
When Firefly first took over the facility, the space was a bare-bones shell with little more than potential. The first months were dedicated to getting the basics right: upgrading electrical systems, securing utilities, fitting lighting and ventilation, and establishing a safe, logical layout for operations.
A modest administrative area was set up to support daily tasks. This space includes basic workstations for project coordination, a small meeting space for discussions, and a welfare area for staff use. While not elaborate, this setup provides the necessary functionality to manage projects and maintain communication with clients and team members.
Welding Bays Designed for Precision and Safety
At the heart of the facility are five fully equipped welding bays, purpose-built to allow our skilled team to conduct high-integrity welding operations to the highest standards.
Each bay has been laid out to accommodate carbon steel, stainless steel, and exotic alloys, with flexibility for working across different joint configurations, orientations, and thicknesses.
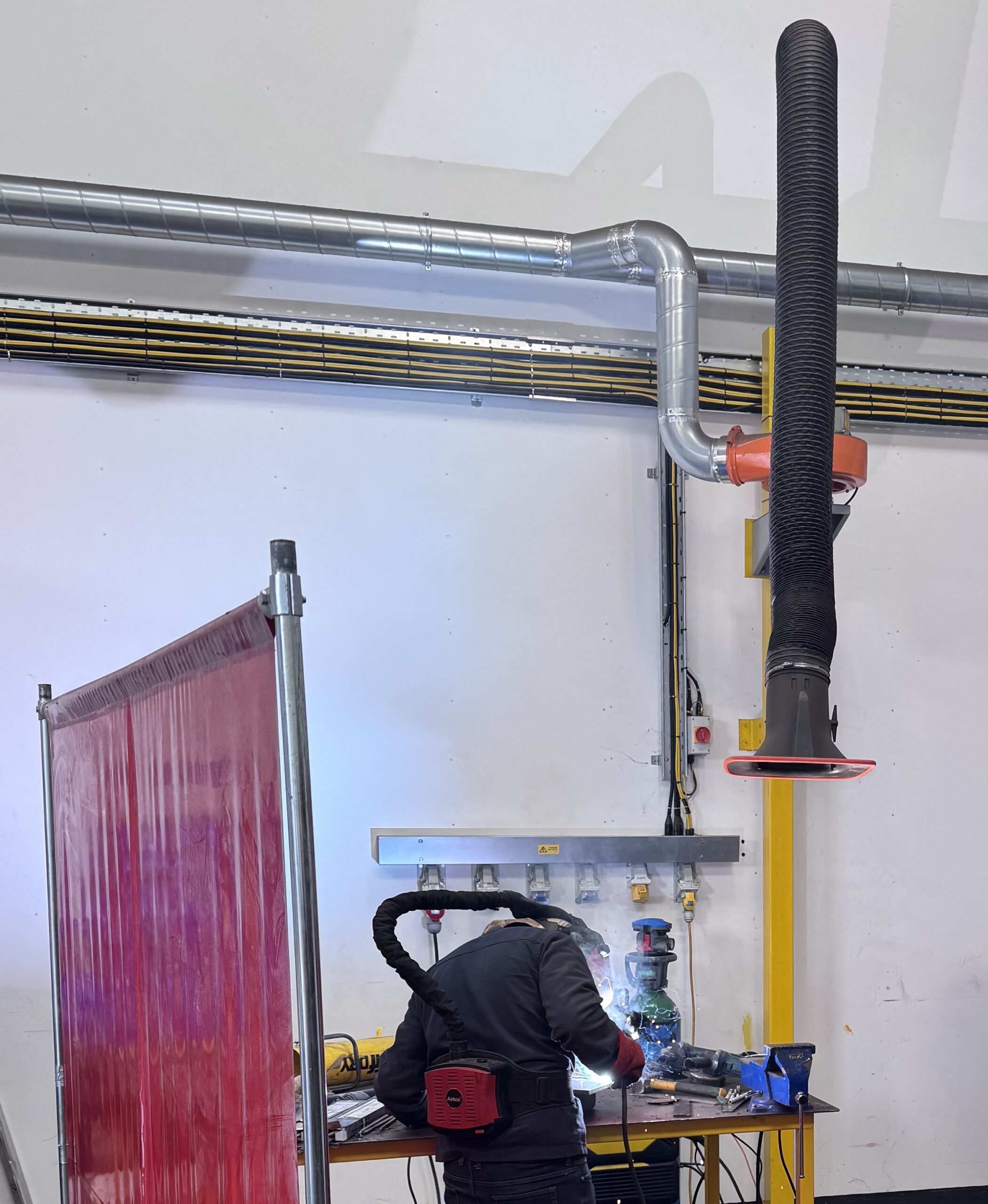
Welding Bay
Equipment includes:
- Multi-process welding machines (TIG, MIG, MMA)
- Firefly Semi-automated welding systems
- Adjustable positioners and manipulators
- Robust ventilation and fume extraction systems
- Secure gas storage and segregated material zones
- Designated workbenches for prep, assembly, and tacking.
Importantly, the bays are arranged to support simultaneous, multi-project working — enabling us to meet tight deadlines without compromising quality.
Product Focus: Welding Habitats and Modular Skids
Since becoming fully operational, the facility has produced a range of specialist fabrication products — most notably, bespoke welding habitats and modular skid systems.
Our in-house welding habitat builds have included confined space cubes, vessel entry systems, and top-access enclosures — all designed to be lightweight, transportable, and easy to deploy in restricted environments. These habitats are fabricated, assembled, and test-fitted at our Wirral site before deployment, giving clients confidence in functionality and compliance before the unit even leaves the workshop.
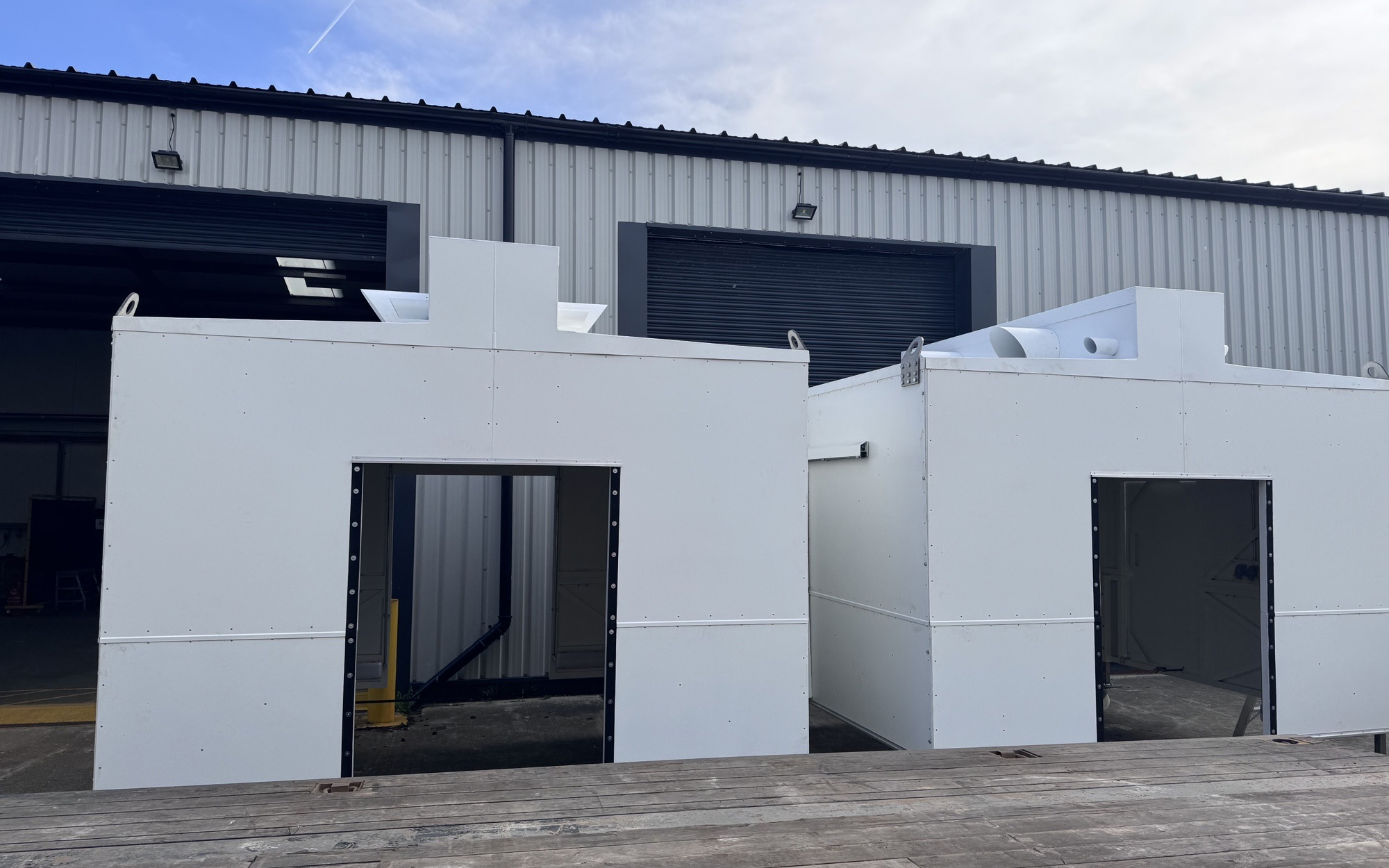
Newly Constructed Welder’s Habitats
We have also seen a rise in demand for modular pipework skids — prefabricated units that consolidate pumps, valves, sensors, and pipework into a single transportable frame. These skids are fabricated, hydro tested, and certified at the facility, minimising time required on client sites and supporting faster commissioning.
Looking Ahead: More Capacity, More Projects
With the facility now fully operational it is ideally suited to expanding the volume and complexity of work it supports — particularly in the areas of modular skid builds, pipework assemblies, and specialised enclosures. The site is equipped to manage both short-run and long-term project work, with flexibility to scale up for multi-skid packages or serial production.