Firefly Welding is proud to announce the successful design, fabrication, and delivery of a series of custom-built welding habitats to a live power station in Shotton, Flintshire. The project represents a significant achievement in modular safety design, highlighting Firefly’s end-to-end capability — from concept and design, through to fabrication, testing, and live-site deployment.
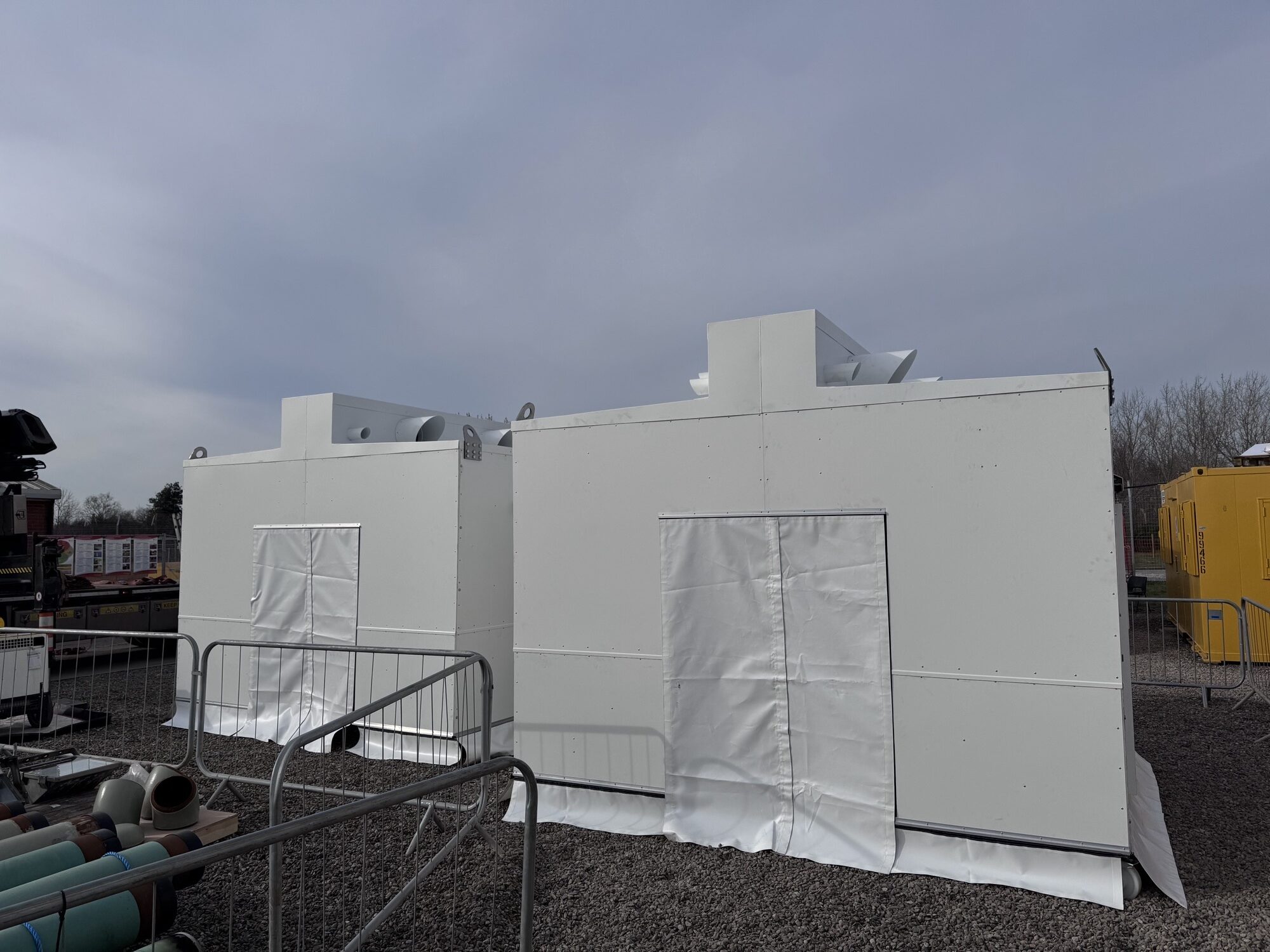
Firefly Welding Habitats
From SolidWorks to Site
The process began in our design office, where we developed a bespoke welding habitat system in collaboration with our client’s project team. Using SolidWorks 3D CAD, our designer was able to build a digital model of the structure, incorporating site-specific requirements and operational feedback from experienced welders. This included details such as fan placements for airflow, access for tooling, and panel adjustments to allow for rapid site assembly.
This early design engagement ensured that once fabrication began at our Wirral facility, the build was seamless. Materials were cut, formed, and welded within our dedicated bays, and key features — such as internal lighting, power for hand tools, and integrated fan systems — were built directly into the frame at this stage. The habitats were then powder-coated to a durable, corrosion-resistant finish before being reassembled for fit-out.
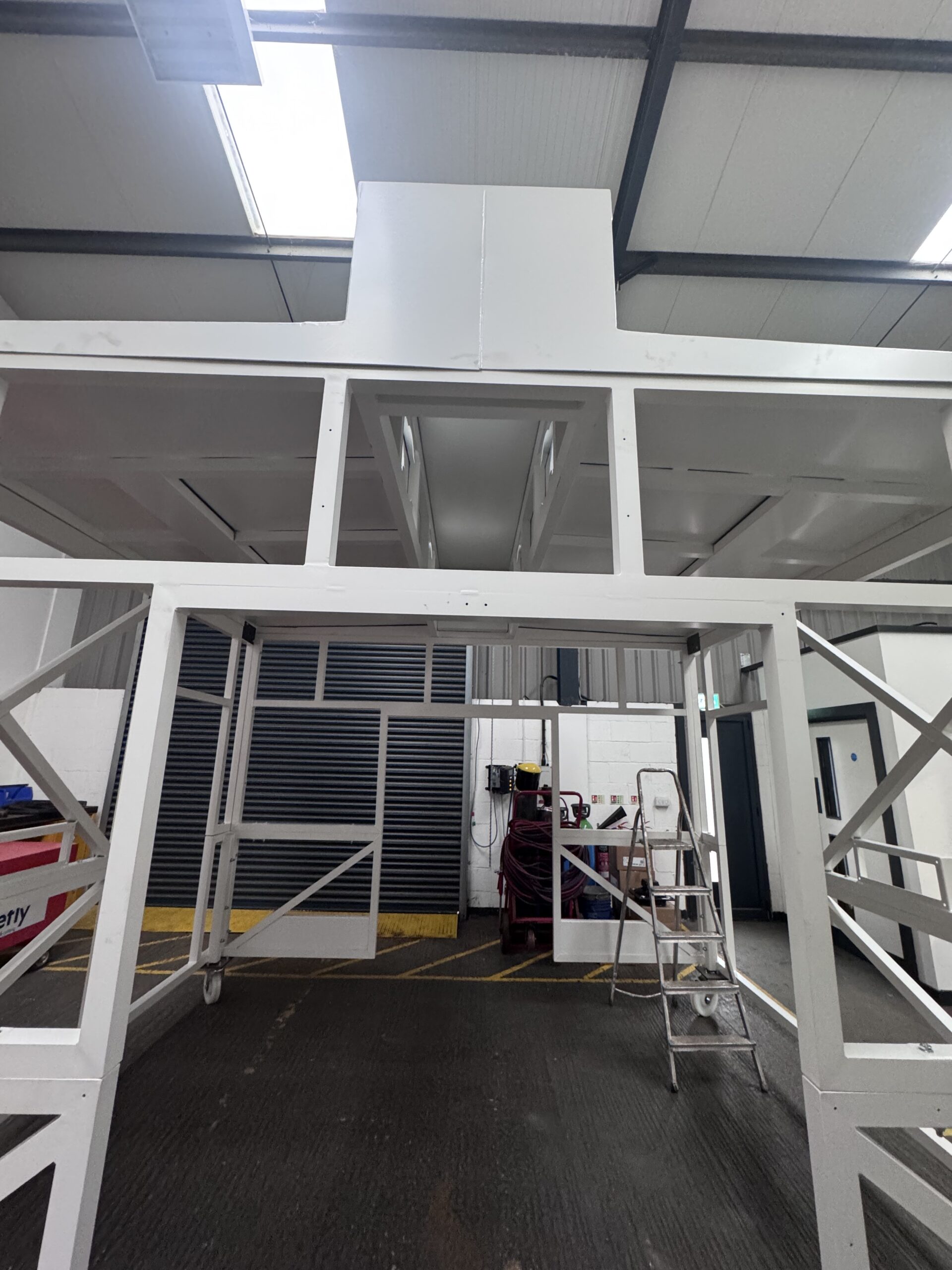
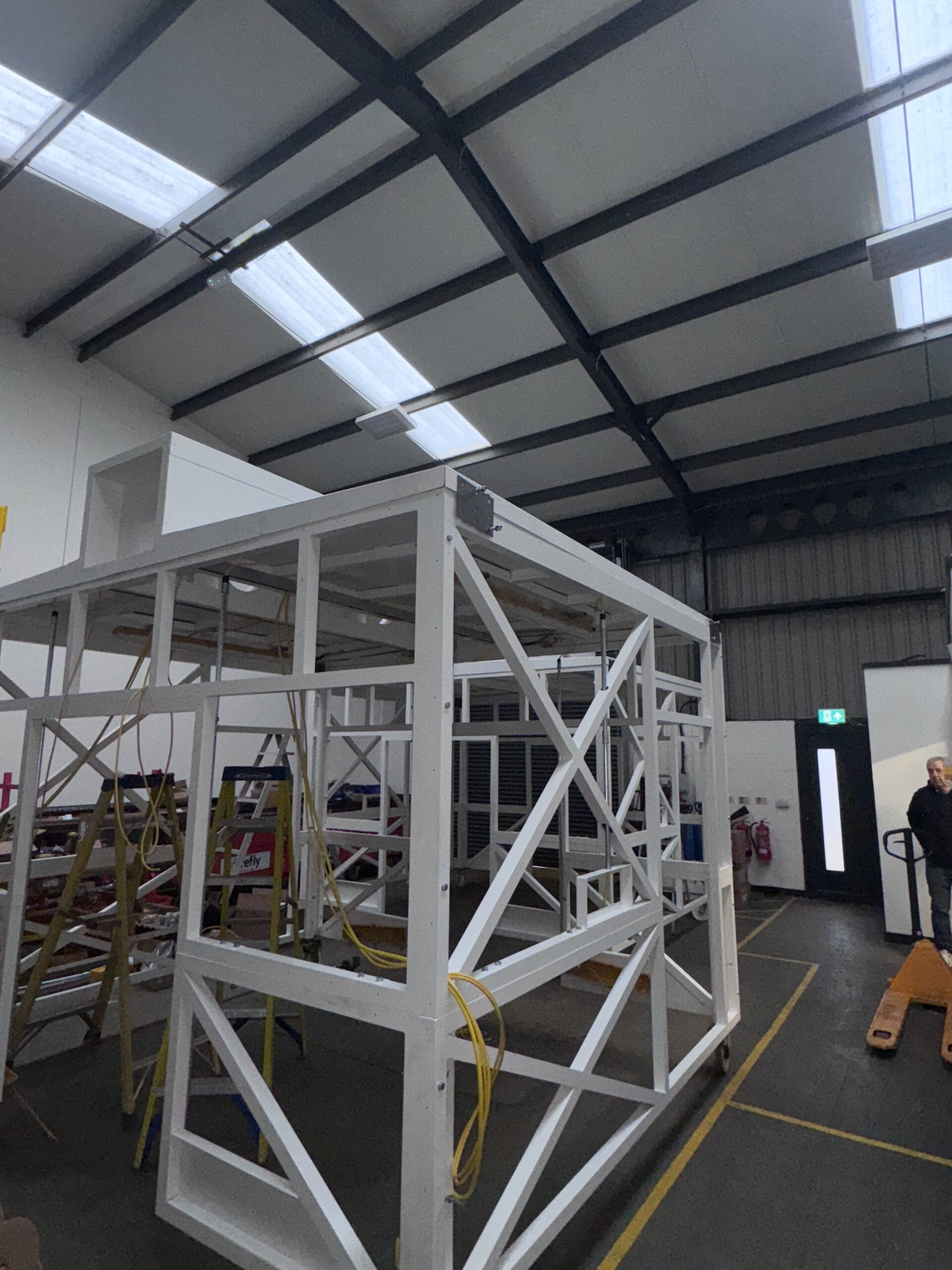
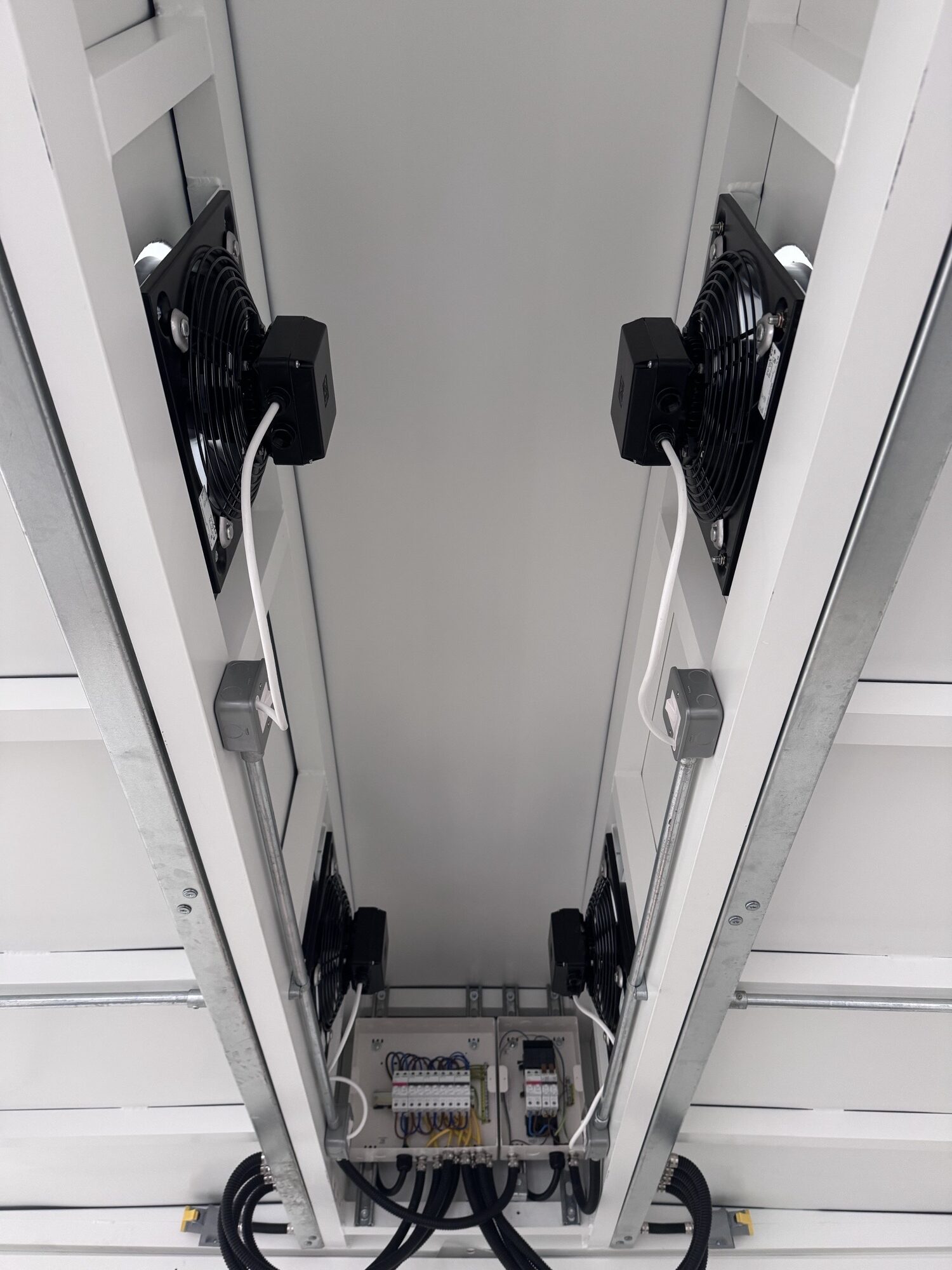
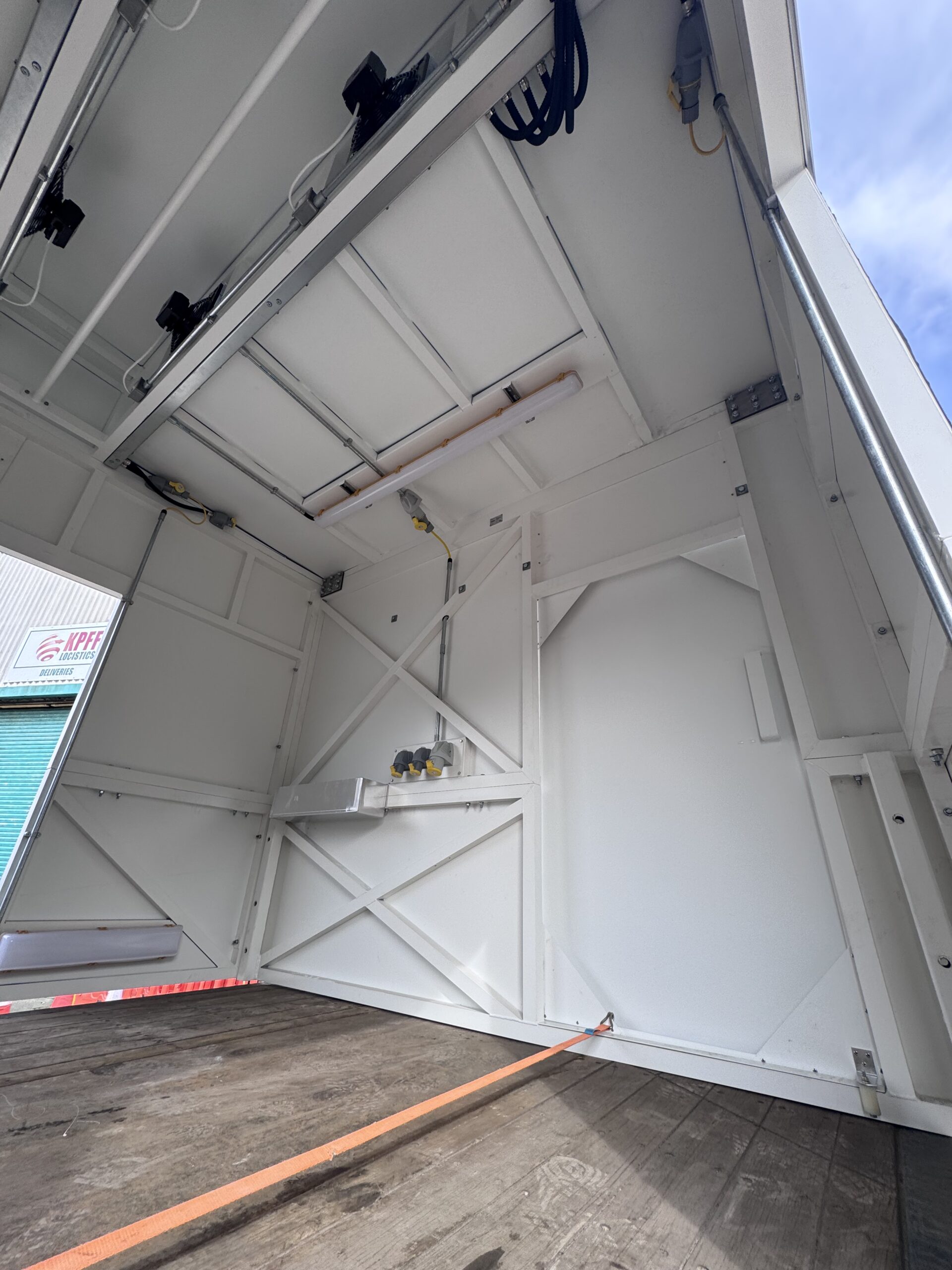
Firefly Welding Habitats during construction
Final quality checks included:
- Full lighting and electrical circuit tests,
- Operational checks on the ventilation system,
- Tooling tests to simulate real site usage,
- Visual and structural inspections to confirm fit and finish.
Deployment to Live Power Station
Working closely with the site’s Authorised Person (AP), Firefly created a detailed lifting and logistics plan for safe transport and installation. A HIAB-equipped vehicle was used to deliver the units, with exclusion zones, lifting gear checks, and communication protocols in place. The deployment was conducted safely, on time, and with no issues raised during final handover.
The success of this deployment has positioned Firefly as a dependable supplier of smart, modular hot work habitats for high-risk environments.
A New Standard for Hot Work Safety
We passionately believe that the way Firefly produces these habitats will become the industry standard in years to come.
Why? Because traditional welding habitats on industrial sites are often cobbled together from ad hoc materials — timber framing, tarpaulin covers, and bolt-on fans or lighting. They are frequently heavy, poorly ventilated, slow to set up, and rarely designed with real consideration for the welder’s comfort or safety.
Our system is different:
- Quality: Each habitat is fabricated to tight tolerances using industrial-grade materials, fully finished with powder coating and fitted with commercial electrical systems. They are designed to last and perform in tough environments.
- Mobility: With standard lift points and modular panel options, the units are easy to transport and position, even in confined or awkward locations. They can be flat-packed or shipped fully assembled depending on access.
- Safety: Built-in fume extraction, spark control, fire-resistant materials, and cable management features make these habitats safer than improvised alternatives. Each unit also accommodates lighting and ventilation compliant with hot work safety protocols.
- Value for Money: Our in-house design and build process reduces turnaround times and avoids reliance on third-party fabricators. The result is a high-quality solution that is competitively priced, durable, and reusable across multiple shutdowns or projects.
- User-Focused Design: These habitats are not just safe — they are comfortable and practical for the people using them. Welders have power where they need it, lighting positioned for visibility, and fans built in to maintain airflow during long shifts.
Looking Ahead
Firefly is now engaging with clients across power generation, petrochemical, and heavy industry sectors to offer these habitat systems as a turnkey solution. Whether it is for a planned shutdown, emergency repair, or ongoing maintenance, we are confident that this modular approach is a smarter, safer way to conduct welding in live or hazardous environments.
As safety standards continue to evolve, we are committed to staying ahead of the curve — not just meeting compliance but setting new expectations for how hot work is supported in the field.